Safety & Training Specialist
Safety & Training Specialist
Provides safety leadership and strategic direction in continuous safety improvement efforts by providing support related to safety and training to production supervisors and management. Will serve as a liaison between the plant and Corporate EHS.
RESPONSIBILITIES
- Direct the safety programs for the site. Recommend the design and implementation of new programs to minimize company losses due to accidents. Measure the effectiveness of programs.
- Calculate and/or track monthly safety-related data. Analyze plant and companywide incidents and trends to assist in reducing exposures.
- Regularly inspect and review plant operations to ensure compliance with state and federal regulations. Report any potential violations and recommend corrections as needed.
- Conduct environmental inspections (ex: hazardous waste, stormwater basins, etc.)
- Conduct and track training sessions, including new hire orientation, annual regulatory topics, and OJT Train the Trainer, on all shifts. Presentations are often in front of large groups.
- Responsible for ensuring that all safety policies, procedures, and practices are reviewed on an annual basis or as changes and updates are required, and are rolled out in a timely manner.
- Facilitate Safety Committee meetings, and maintain minutes.
- Conduct monthly safety audits. Include appropriate members of the management team. Document corrective actions. Conduct safety inspections and procedural audits in the plant and have the skills, knowledge, and ability to take immediate corrective action if required.
- Participate in incident investigations with supervisors/managers. Investigate all safety-related incidents, review incident reports and complete necessary reports for insurance carriers, risk management systems, and corporate safety.
- Ensure monthly chemical inventories are conducted and documented by chemical suppliers. Complete related annual environmental reports, including, but not limited to Tier II and Form R.
- Coordinate annual hearing testing, evacuation drills, and other regulatory tasks as directed.
- Assist in the development of “task-based” LOTO Procedures.
- Regularly meet with the Maintenance Department to prioritize safety work orders.
- Maintain Hazard ID and Safety Observation Logs and follow up on items.
- Update the Safety Data Sheets (SDS) and other clerical tasks related to safety programs
- All GLC employees are expected to perform any assignment or job task according to the stated safety policies and procedures.
- All GLC employees are expected to produce and promote our products and services in a manner that exceeds the quality and value expectations of our customers and consumers by adhering to Good Manufacturing Practices, Policies, and Procedures outlined in our Safe Quality Food Program.
- Other responsibilities as assigned by the manager.
REQUIRED EDUCATION, EXPERIENCE AND SKILLS
- Bachelor’s Degree from an accredited institution.
- Experience working with manufacturing processes and related equipment.
- Experience with Microsoft Windows Applications/Microsoft Office Suite (Excel, Work, PowerPoint).
- Minimum of 2 years of experience implementing safety programs.
PREFERRED EDUCATION, EXPERIENCE AND SKILLS
- Bachelor’s Degree in Industrial Engineering, Occupational Safety and Health, Industrial Hygiene. or related Safety/Environmental/Engineering discipline.
- 3-5 years of experience leading safety programs.
- OSHA 10 Hour / OSHA 30 Hour Certification.
- EPA RCRA Waste Management Certification.
- First Aid/CPR Certification (Bi-Annual Course).
- DOT Hazardous Materials Transportation Certification (Tri-Annual Course, Ground Shipments).
- While the majority of the tasks will be conducted on first shift, candidates must be prepared to provide support on all shifts, particularly for training-related items.
- Must be able to evaluate conditions and behaviors by periodically walking through the plant. Must be able to climb stairs, and ladders, and work at heights.
WORKING CONDITIONS
- Work is mainly performed in an office setting, with some time spent in a manufacturing environment.
- Occasional exposure to industrial operations including temperature extremes from approximately 35ºF to 100ºF; noise levels in excess of 85 dB; moisture and moving machinery.
Great Lakes Cheese is an Equal Opportunity Affirmative Action Employer AA/M/F/V/D.
Images
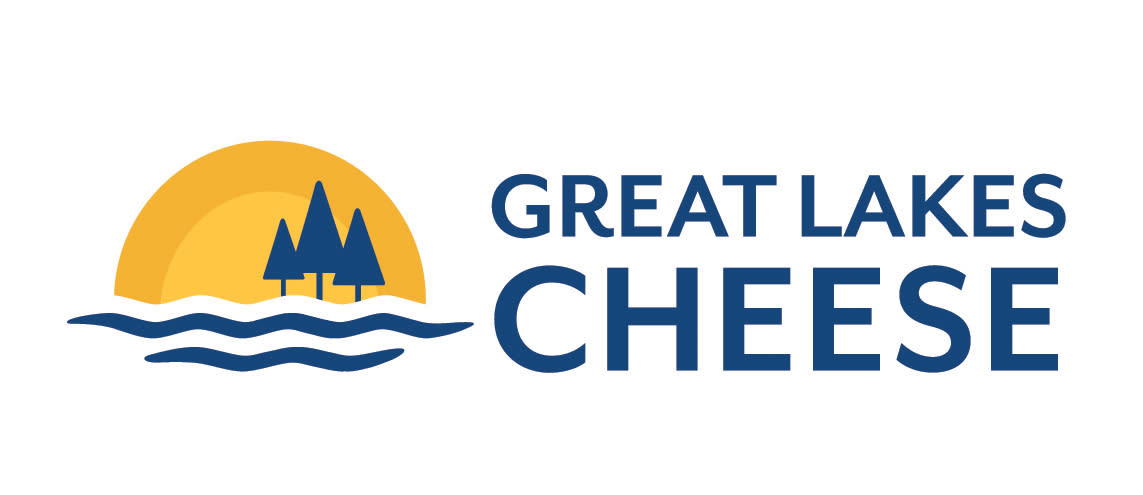
Additional Info
Job Type : Full-Time
Education Level : Bachelors Degree
Powered By GrowthZone